Making a sidewalk is a lot easier than people think. It's also a lot cheaper to do all your own labor. First we need to decide how wide we want to make it and how long. We also need to know how deep into the ground we want to dig.
It's much easier if you don't have to dig very deep at all when starting a sidewalk, but this depends on your building site. For instance, if you're putting in a new sidewalk before you dump the top soil for a new lawn then you will want to keep the sidewalk on top of the ground. If you are setting the sidewalk into an existing lawn or walk area, then you will need to dig down an inch or two so the sidewalk isn't too high. Sidewalks that are too high are tripping hazards because they stick up too far.
3 Circular Saw
Let's say our sidewalk is going to be four feet wide and thirty feet long. This will be a sidewalk where we'll need to dig into the ground exactly two inches. We need to measure across the sidewalk area which we already know is forty-eight inches, but we also need to dig the extra area where the forms will go. The forms for sidewalks are often just 2x4 studs. They are cheap and really easy to work with.
The measurement across the sidewalk will include the thickness of a 2X4 stud on each side. The thickness of each stud is an inch and a half, so add 3 inches onto the width of the sidewalk. This will give us an area of 51 inches to dig. Of course, we can always dig a much wider area and just backfill the dirt once the sidewalk is done.
The excavated area will be 51 inches wide by thirty feet long. Sidewalks are usually dug out with a shovel because of the shallow depth. You will need to make sure the entire area is level and you may need to tamp the dirt where the cement will be poured. At this point we can start setting in the forms. The best way to join two 2X4 studs is by nailing a 2X4 block on the outside of the forms where the joint is. This will keep them secure. Next, make sure the forms are even with a consistent measurement of 48 inches the entire length.
You won't need to use rebar like you do when pouring foundations. If you're making a small sidewalk, then you can buy bags of ready mix, add water and pour it in, but for most projects, you will want to call the cement company to deliver and pour the cement. The cement needed for sidewalks is a smoother type of cement than foundations. Foundation cement is called "5-bag mix, but sidewalk cement is "six-bag mix. It has a higher cement content and uses smaller aggregate material.
The cement company will know what to do when you tell them the cement is for a sidewalk. They will ask you for the dimensions of your project and they will calculate the amount of cement needed. Cement is calculated and sold by square yards. Let's take our measurement as an example. Our sidewalk is thirty feet long, four feet wide, and four inches deep. So our square footage is 120 square feet by four inches deep. Let's convert this to square yards by dividing 120 by 27. There are 27 cubic feet in a square yard. This gives us 4.44 square yards, but we still have to divide that by 3 because the sidewalk isn't a foot thick, it is only four inches, which is a third of a foot. So our final number is about one and a half yards of cement needed to pour the sidewalk. The price of cement varies by location, but if you live fairly close, you should be able to get it for around per yard.
Now, we're ready to pour the sidewalk. The cement truck will pour the cement, but you will need to shovel it around to get it even against the forms. You will need to get the cement evenly into the forms. Jab the cement constantly to break any air bubbles. Once the cement is where you want it, you will need to make it smooth. You can buy a screed or you can just use a level 2X4 to run across the top of the cement. This will make it basically smooth.
Once you have the surface fairly smooth, you will need to use a float or a long trowel to bring the fine cement to the surface. This will make a very smooth surface and will make the rougher aggregate material sink beneath the surface. You will want let this dry for a few hours before brushing the surface with a shop broom. Brushing will give the sidewalk some traction so you don't slip on the smooth surface. Be careful not to overdo the brushing.
After about three days, you can remove the forms and start to back fill the edges of the sidewalk so they are even with the lawn or ground. Ideally, we like to have the side walk about a half inch higher than the lawn.
For the final step in the sidewalk process, we need to cut sections in the concrete so it doesn't crack with the movement of the ground underneath. You can rent a concrete cutter or use a concrete blade on a circular saw and cut across the sidewalk every ten feet or so. This will give the sidewalk flexibility during expansion and contraction of the soil.
That's basically how to make your own sidewalks. We can usually save about two-thirds the cost of a professionally poured sidewalk by doing it ourselves.
Christmas Sales Forrest WW07Q307100 Woodworker II 7-1/4-Inch 30 Tooth 5/8-Inch Arbor 3/32-Inch Kerf Circular Saw Blade 201
Dec 29, 2011 16:16:30
Click for larger image and other views
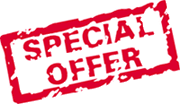
Christmas Sales Forrest WW07Q307100 Woodworker II 7-1/4-Inch 30 Tooth 5/8-Inch Arbor 3/32-Inch Kerf Circular Saw Blade Feature
- Forrest Saw Blades dampener helps kill saw scream-whistle from a vibrating blade surface.
- Dampen out motor and belt vibrations from being transmitted up to the rim of the teeth.
- Greatly reduce cutting noise.
- Hold blade rigid and true for better cuts on your machine.
- Are hardened and precision ground flat within .001" to keep your blade true.
Christmas Sales Forrest WW07Q307100 Woodworker II 7-1/4-Inch 30 Tooth 5/8-Inch Arbor 3/32-Inch Kerf Circular Saw Blade Overview
With this all purpose blade for tables saws you can rip and crosscut 1" - 2" rockhards and softwoods resulting in a smooth-as-sanded surface. With 20 DEG face hook, ply-veneers will crosscut with no bottom splinter at moderate feed rates. Double hard and 40% stronger C-4 carbide will give up to 300% longer life between sharpenings. Ends blade changing (one blade does rip, combo and crosscut). Ends second-step finishing. Ends cutting 1/16" oversize to allow for resurfacing. Buy and sharpen one blade instead of 3, (24T rip, 50T combination, 80T crosscut).SAVE NOW on Christmas Sales Offers below!
Available In Stock. |
This Christmas Forrest WW07Q307100 Woodworker II 7-1/4-Inch 30 Tooth 5/8-Inch Arbor 3/32-Inch Kerf Circular Saw Blade is cheap and shipping as well. |
Price : Click to Check Update Prices Please. |
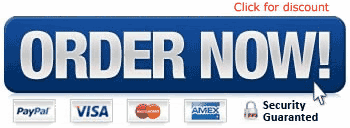